The laser cutting method of aluminum alloy is becoming more and more perfect


The laser cutting method of aluminum alloy is becoming more and more perfect
Aluminum alloys are widely used in semiconductor and microelectronic industries because of their good physical and chemical properties and
excellent mechanical properties. With the development of modern industrial products towards high strength, light weight and high performance, the
laser cutting method of aluminum alloy is also developing towards precision, high efficiency and flexibility. Laser cutting has become an important
method for precision machining of aluminum alloy because of its advantages such as narrow slit, small heat affected zone, high efficiency and no
mechanical stress.
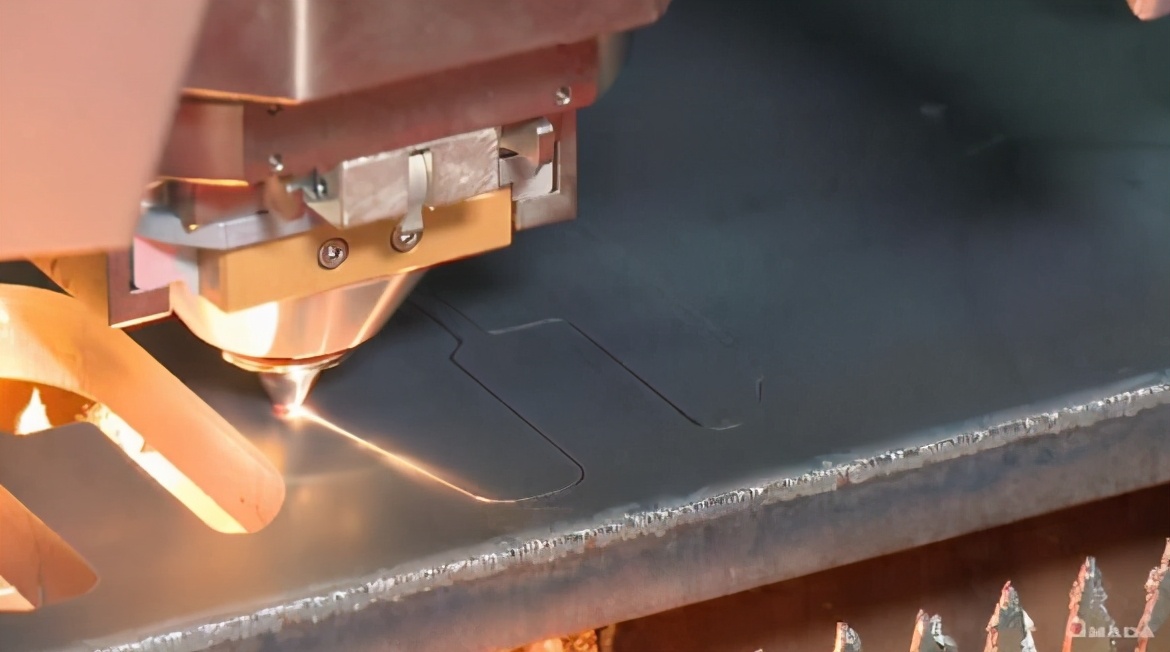
The existing laser cutting of aluminum alloy is generally cut by cutting head and auxiliary gas. The mechanism of the cutting is that laser focuses
on the aluminum alloy, and the molten material is blown away by high energy gasification and melting of aluminum alloy with high pressure
auxiliary gas.
This cutting method mainly uses two kinds of lasers with wavelength of 10640nm and 1064nm, which belong to the infrared wavelength range. In
the precision cutting of aluminum alloy sheet with the cutting dimension precision of micron level, due to its large spot spot and large thermal
influence area, it is easy to generate slag and microcracks at the cutting edge, which will ultimately affect the cutting accuracy and effect.
The aluminum alloy laser cutting system and method realize the cutting of the workpiece to be cut in a non-contact way by using the smaller pulse
width and shorter wavelength of the laser beam, so as to avoid the contact stress loss of the workpiece to be cut by mechanical method, as well as
the problems of microcracks and slag hanging caused by thermal machining in the cutting process; The workpiece to be cut is fixed horizontally by
using a specific fixture. While keeping the cutting seam position suspended, the cutting area of the workpiece to be cut is supported from the back
to prevent the cutting edge effect from being damaged by stress caused by falling at the moment of cutting; Through the circulating cooling water in
the water tank device, the cutting workpiece is cooled to reduce the impact of heat on the surrounding materials and further improve the cutting
quality; Through the combination of multiple cutting paths, the cutting is carried out to expand the cutting seam width and improve the cutting
efficiency.