Artificial Intelligence Reshapes 3D Printing —— Ushering in the Era of Additive Manufacturing 4.0


AI is driving a revolution in 3D printing technology. Generative AI and topological optimization technologies have broken through the limitations of traditional design, improving part precision by 30% and reducing energy consumption by 25%. Laser automated production networks dynamically adjust parameters via AI, ensuring a precision of 0.05mm per layer. One production line has seen its efficiency quadruple, with material utilization exceeding 98%.
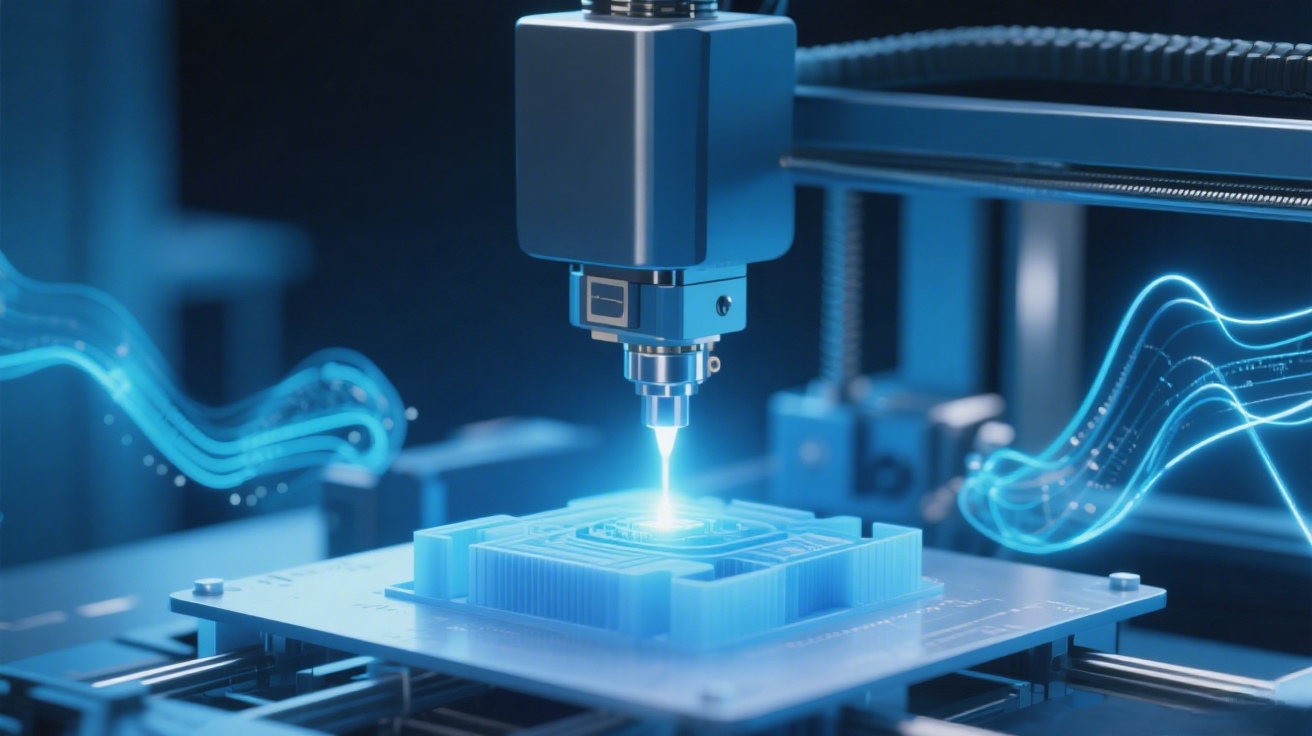
Applications across multiple sectors are delivering remarkable results. In aerospace, AI-optimized laser technology has reduced the weight of turbine blades by 40% while increasing their fatigue resistance by 25%. In automotive manufacturing, AI-driven design has shortened mold development cycles from months to 72 hours, cut costs by 50%, and achieved 35% lightweighting for battery brackets. In healthcare, custom implants have realized biomimetic replication of trabecular bone, boosting postoperative joint mobility by 40%.
Technological synergy is accelerating breakthroughs. Intelligent lasers integrated with adaptive algorithms have doubled the efficiency of multi-laser equipment. Industrial internet software systems, leveraging digital twin technology, have advanced equipment failure prediction by 4 hours, reduced unplanned downtime by 70%, and shortened process debugging time by 80%.
Looking ahead, edge computing and digital twins will propel 3D printing into an "self-optimization era." It is projected that the global additive manufacturing market will exceed $60 billion by 2030, with AI contributing over 40% of this growth. Through a full-stack layout of "hardware, software, and services," laser technology will redefine the cost and efficiency boundaries of manufacturing, ushering in a new era of "Manufacturing as a Service."
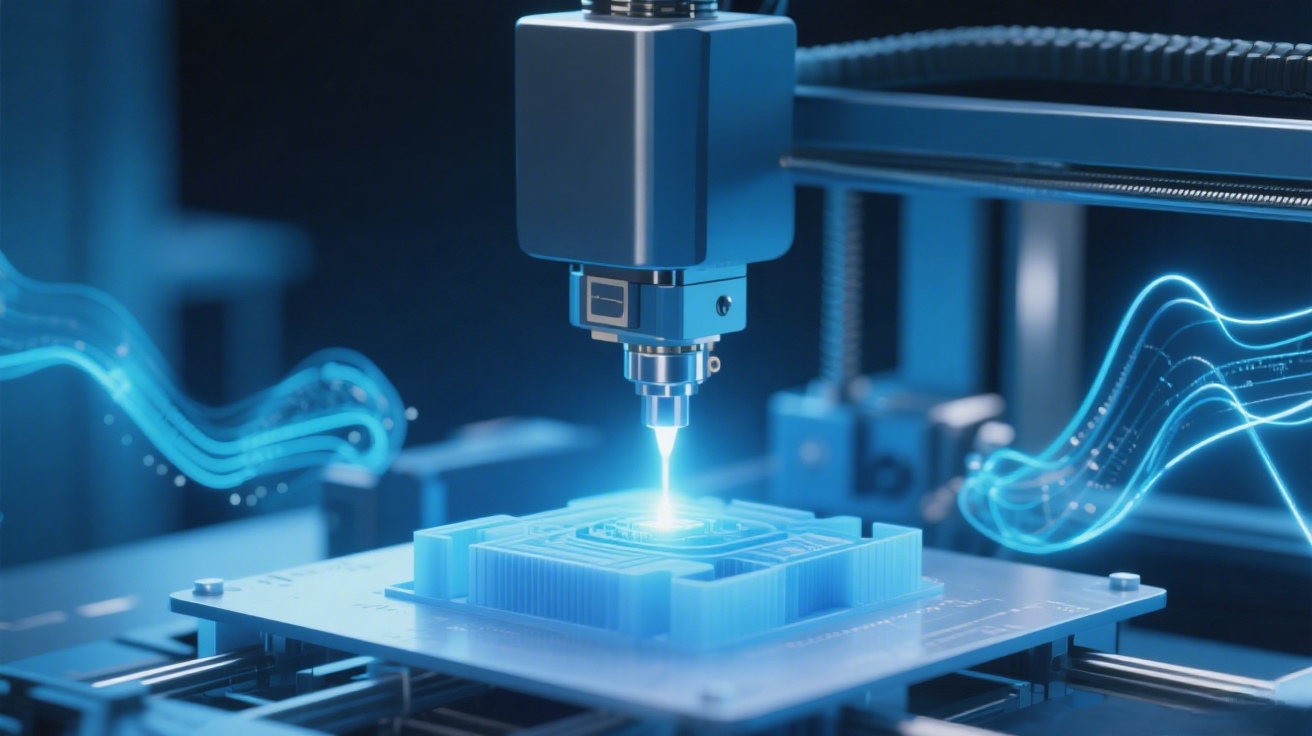
Applications across multiple sectors are delivering remarkable results. In aerospace, AI-optimized laser technology has reduced the weight of turbine blades by 40% while increasing their fatigue resistance by 25%. In automotive manufacturing, AI-driven design has shortened mold development cycles from months to 72 hours, cut costs by 50%, and achieved 35% lightweighting for battery brackets. In healthcare, custom implants have realized biomimetic replication of trabecular bone, boosting postoperative joint mobility by 40%.
Technological synergy is accelerating breakthroughs. Intelligent lasers integrated with adaptive algorithms have doubled the efficiency of multi-laser equipment. Industrial internet software systems, leveraging digital twin technology, have advanced equipment failure prediction by 4 hours, reduced unplanned downtime by 70%, and shortened process debugging time by 80%.
Looking ahead, edge computing and digital twins will propel 3D printing into an "self-optimization era." It is projected that the global additive manufacturing market will exceed $60 billion by 2030, with AI contributing over 40% of this growth. Through a full-stack layout of "hardware, software, and services," laser technology will redefine the cost and efficiency boundaries of manufacturing, ushering in a new era of "Manufacturing as a Service."